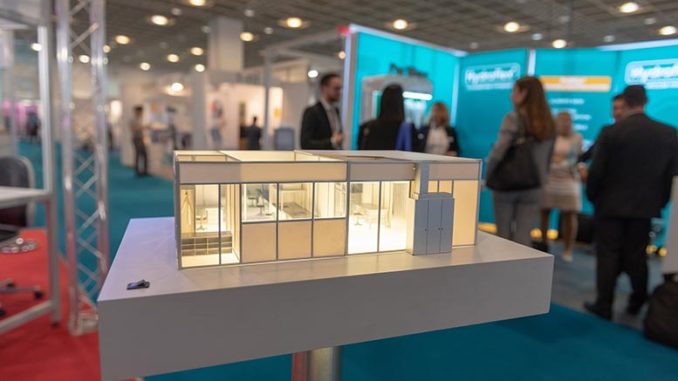
Worum es bei einer Kostenbetrachtung für eine reine Fertigung geht, verdeutlicht das folgende Beispiel: „Ein Automobilzulieferer fragte einen Reinraum mit mehreren hundert Quadratmetern Grundfläche und einer Klassifizierung nach ISO 7 an“, berichtet dazu Joachim Ludwig, Colandis GmbH, Kahla. „Eine erste Kostenschätzung ergab eine Angebotssumme von zirka 450.000 Euro. Nach dem Besuch bei diesem potenziellen Kunden stellte der Vertriebsmitarbeiter fest: Die im Reinraum aufzustellende Fertigungsanlage wäre bestens für eine Mini-Environment-Lösung geeignet; es fehlten nur noch die notwendigen Filter-Fan-Module zum kombinierten Ansaugen, Filtern und Einblasen von Luft. Das Ergebnis war, dass dieser Automobilzulieferer nicht in den Reinraum, sondern in die intelligente Aufrüstung seiner Fertigungsanlage investiert hat.
Als Quintessenz ergibt sich aus diesem Beispiel: einfach einmal die Perspektive wechseln! Alle Überlegungen starten nicht bei einem Reinraum (Länge mal Breite mal Höhe plus bestimmte Spezifikationen gemäß der Norm ISO 14644), sondern beim Produkt und der gewünschten Qualität.
Kostengünstiges Labor für die Herstellung von Zytostatika
Oft führt dieser Perspektivwechsel zu Mini-Environments – im Folgenden ein Beispiel aus dem Pharma-Bereich.
„Im Anwendungsbereich von pharmazeutischer Herstellung durch Krankenhaus und öffentliche Apotheken nehmen die Anforderungen von Amtsapothekern und Regierungspräsidien zu“, erläutert Egon Buchta, Ingenieurbüro & Reinraumservice Egon Buchta GmbH, Wannweil. „Obwohl die Apothekenbetriebsordnung beispielsweise die Herstellung von Zytostatika und von krebserzeugenden, erbgutverändernden oder fortpflanzungsgefährdenden Arzneimitteln grundsätzlich in drei Varianten zulässt, fordern die Behörden mehr und mehr die aufwändigste von ihnen: Herstellung in Reinraumklasse A in einer Klasse-B-Umgebung. Dies bedeutet höhere Volumenströme, mehr Räume und Schleusen, höhere Textil-Kosten, längere Zeiten für die Einschleusung von Mitarbeitern und Material, längere Messzeiten – kurz: Kostensteigerung an allen Ecken und Enden.“
Dennoch gibt es Wege zu kostengünstigeren Lösungen. Ein neues Zytolabor kann beispielsweise auch mit der Variante „Reinraumklasse A in Klasse D“ geplant werden. Dafür ist es notwendig, dass die Arbeiten im Inneren eines Mini-Environments („Klasse-A-Glovebox“) mit relativ dicken Handschuhen („neoprenähnlich“) durchgeführt werden. Im Ergebnis reduziert sich die benötigte Reinraumfläche, und es ist ein geringerer Luftvolumenstrom erforderlich.
Hohes Potenzial bietet die Optimierung der Belüftungstechnik
Vom Pharmabereich zur Mikrochipproduktion: „Sie ist zurzeit von zwei Trends geprägt“, erklärt Josef Ortner, Ortner Reinraumtechnik, Villach. „Generell werden Luftmengen reduziert, und zur weiteren Verminderung des Energiebedarfs setzt man häufiger multitaskingfähige Komponenten ein – zum Beispiel Filter, Brandmelder und Deckenbeleuchtung in einem.“
Es gibt zahlreiche Ansätze, um die Luftmenge zu verringern. Zum Beispiel führen Drallauslässe an Lüftungsgittern zu unerwünschten Verwirbelungen. Eine laminare Strömung wird dann erschwert bis verhindert. Zuweilen reicht es, ein Gitter durch eine Längsschürze zu ersetzen – sogleich reduzieren sich die umgewälzten Luftmengen. Wer die Luftwechselzahlen vermindert, senkt seinen Energieverbrauch, erhöht die Standzeit seiner Filter und auch den Geräuschpegel im Betrieb. Man muss dabei allerdings die automatisch längeren Erholzeiten gegenrechnen. Darunter versteht man die Zeit, in der die Partikelbelastung ausgehend von einem definierten Zustand auf 1 Prozent zurückgeht.
Für zusätzliche Optimierungen empfiehlt sich eine Visualisierung der Strömungsverhältnisse im Reinraum mit einer neuen 3D-Videotechnik unter Verwendung einer VR-Brille. Auch lohnt es sich unter dem Gesichtspunkt der Energiekosten praktisch immer, die Dichtigkeit der Gebäudehülle oder eines einzelnen Reinraums zu bestimmen (z.B. Blower-Door-Test).
Luftaustauschmengen lassen sich zukünftig unter Verwendung intelligenter Zugangskontrollsysteme sogar an die Anzahl der Mitarbeiter anpassen. Dann ist es nicht mehr nötig, dass sich der Betreiber bei der Partikelkonzentration Sicherheitsreserven von mehreren 100 Prozent lässt – was keine Seltenheit ist. Josef Ortner erinnert sich: „Bei einem Kunden haben wir alle Prozessanlagen analysiert und im Endeffekt durch verschiedene Feinsteuerungsmaßnahmen jährlich 40.000 Kubikmeter Prozessluft eingespart.“
Bild & Text: cleanzone.messefrankfurt.com