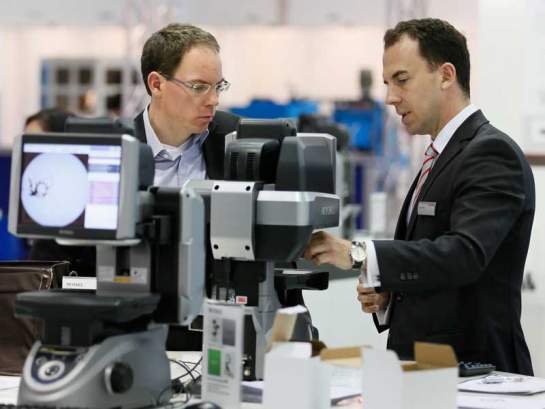
Die Bedeutung der Windenergie an der Stromerzeugung nimmt weiter zu: 2015 steigerten die Windparks in Deutschland im Vergleich zum Vorjahr ihre Leistung um rund zwei Drittel. Nach Angaben des Fraunhofer ISE erzeugten die Windräder zwischen Nordsee und Alpen im letzten Jahr insgesamt 85,4 Milliarden Kilowattstunden Strom. Der Windenergiebranche zufolge betrug der Anteil der Windkraft über 13 Prozent an der Bruttostromerzeugung und rund 14,5 Prozent am Stromverbrauch.
Der bei weitem größte Teil der Stromerzeugung entfällt auf Windkrafträder, die an Land installiert sind. Offshore-Windenergieanlagen (OWEA) konnten in Deutschland nach dem Rekordjahr 2014 aber auch 2015 neue Bestmarken erzielen. So gingen auf See 546 Windenergieanlagen mit einer Leistung von 2.282,4 Megawatt (MW) erstmals ans Netz. Ende Dezember 2015 lieferten damit insgesamt 792 OWEA mit einer Gesamtleistung von 3.294,9 MW Strom ins Netz (Quelle: Deutsche WindGuard „Status des Offshore-Windenergieausbaus in Deutschland“). Für 2016 rechnet die Branche mit einem Zubau von weiteren 700 MW.
Gegenüber der Onshore-Windenergie liegen die Kosten der Offshore-Windenergienutzung höher, weil die technischen Herausforderungen deutlich größer sind. Denn die OWEA müssen im Wasser gegründet, verkabelt, installiert und betrieben werden. Zudem sind die Anlagenlasten im Betrieb größer als an Land, Wartung und Instandsetzungsarbeiten deutlich aufwändiger. Weil auf See aber in der Regel höhere Winderträge erreichbar sind, können sich auch OWEA rechnen. Der prinzipielle Nachteil der größeren Entfernung zwischen Stromerzeugung und Verbrauch hat für eine Branche – die Kabelhersteller – sogar Vorteile: Um den Strom vom Windrad zur Steckdose zu bringen, sind bei OWEA große Kabellängen erforderlich.
Als ein Beispiel für die notwendige Verkabelung sei hier der im Oktober 2015 in den Regelbetrieb genommene Offshore-Windpark „Amrumbank West“ genannt. Auf einer Fläche von 32 Quadratkilometern rund 35 Kilometer nordwestlich von Helgoland wurden in Wassertiefen von 20 bis 25 Metern 80 einzelne Windenergieanlagen, eine Umspannplattform und eine Messplattform errichtet. Die Windenergieanlagen verfügen über eine Nennleistung von jeweils 3,6 MW und einen Rotordurchmesser von 120 Metern. Mit ihnen kann Strom für 300.000 Haushalte erzeugt werden.
Der Windpark erhielt eine rund 100 Kilometer lange Innerparkverkabelung von den 80 Windenergieanlagen zur Umspannplattform, die den Dreiphasenwechselstrom (Drehstrom) von 33 Kilovolt (kV) auf 155 kV transformiert. Der Strom wird dann über ein Exportkabel zur 8 Kilometer entfernten Konverter-Plattform geleitet, die den Dreiphasenwechselstrom auf die Spannungsebene ± 320 kV transformiert und anschließend in Gleichstrom umwandelt. Per Hochspannungs-Gleichstrom-Übertragung (HGÜ) findet anschließend die Weiterleitung über ein am Meeresboden verlegtes Seekabel zum 85 km entfernten Büsum und von dort weitere 45 Kilometer bis zum Netzverknüpfungspunkt in Brunsbüttel statt, wo der Gleichstrom wieder in Drehstrom zurückgewandelt wird.
Deutlich kleiner ist der erste deutsche Offshore-Windpark „alpha ventus“, der mitten in der Nordsee seit Ende 2009 steht. Die von alpha ventus produzierte Strommenge reicht für die Versorgung von bis zu 50.000 Haushalten. Er besteht aus zwölf Windenergieanlagen mit einer Nennleistung von je 5 MW und einem Offshore-Umspannwerk, das den Transformator und sämtliche elektrotechnischen Anlagen beherbergt.
Auch hier legt der Strom von der Erzeugung bis zum Verbraucher einen langen Weg zurück. Innerhalb des Windparks wird der Strom von den Windenergieanlagen zunächst mit 33 kV-Seekabeln zum Offshore-Umspannwerk geführt. Dazu wurden rund 16 Kilometer Kabel mindestens 60 Zentimeter tief im Meeresgrund vergraben. Nach der Transformation im Offshore-Umspannwerk auf 110 kV wird die elektrische Energie durch ein rund 60 Kilometer langes und in den Meeresboden eingegrabenes, armdickes Seekabel über die Insel Norderney bis zur norddeutschen Küste transportiert. Als Einspeisepunkt in das deutsche Stromübertragungsnetz fungiert das Umspannwerk Hagermarsch. In die Seekabel sind zusätzliche Datenleitungen aus Glasfaser integriert, die den Anschluss des Windparks an moderne Kommunikations- und Überwachungssysteme ermöglichen.
Steuerung und Überwachung an Land
Gesteuert und überwacht werden OWEA in der Regel von Land aus. Im Fall alpha ventus ist die Leitstelle in der Stadt Norden im Landkreis Aurich untergebracht. Hier laufen alle Informationen und Daten zusammen. Auf mehreren Bildschirmen wird der Betriebszustand des Windparks in Echtzeit dargestellt – über Bilder, Karten, Grafiken und Zahlen. Zu den erfassten Betriebsdaten zählen unter anderem Windgeschwindigkeit, Leistungsabgaben, Drehzahlen, Öltemperaturen und Ausrichtung der Gondeln. Die Daten werden mit Hilfe eines „Condition Monitoring System“ (CMS) überwacht und ausgewertet, um frühzeitig ungewöhnliche Werte erkennen und Maßnahmen ergreifen zu können. Die Betriebsführer koordinieren und überwachen außerdem die Einsätze der Serviceteams im Windpark. Über eine steuerbare und mehrere fixe Webcams verfolgen die Betriebsführer auch die Helikopterflüge und Schiffsbewegungen im Windpark.
Große Entfernungen gilt es auch beim Offshore-Windpark Sandbank zu überbrücken. Rund 90 Kilometer vor Sylt und 110 Kilometer von der Küste entfernt werden hier in 24 bis 33 Meter Wassertiefe 72 Windturbinen mit 4 je MW Nennleistung errichtet, die bei einer Jahresstromproduktion von 1,4 Terawattstunden den Verbrauch von etwa 400.000 deutschen Haushalten abdecken können. Bei dem 60 Quadratkilometer großen Windpark beträgt die Kabellänge von der Konverterstation bis zur Küste 165 Kilometer. Weitere 45 Kilometer kommen von der Landungsstelle des Kabels in Büsum bis zum Umspannwerk dazu. Der Offshore-Windpark Sandbank soll 2017 in Betrieb gehen.
Bei der Innerparkverkabelung wird der Strom von den 72 Windenergieanlagen zum parkinternen Umspannwerk transportiert. Jeweils neun Windenenergieanlagen sind über einen Kabelstrang mit dem Umspannwerk verbunden. Jeweils zwei Stränge können so miteinander verbunden werden, dass auch bei einem Kabelschaden der Betrieb der Anlagen gesichert ist. Insgesamt werden rund 96 Kilometer Kabel mit zwei verschiedenen Querschnitten (630 und 185 Quadratmillimeter) innerhalb des Windparks verlegt. Die Kabel enthalten zudem Lichtwellenleiter, die den Datenaustausch zwischen jeder Windenergieanlage und dem Umspannwerk sowie die Fernsteuerung und Überwachung des Windparks vom Kontrollzentrum im dänischen Esbjerg ermöglichen. Die Kabel werden zunächst auf dem Seeboden abgelegt und später in Tiefen von mindestens 0,6 Meter bis zu mehr als einem Meter in den Nordseeboden eingespült. Die Verlegearbeiten führt ein spezielles Kabelverlegeschiff aus, das auch den Transport der Kabel vom Hersteller in Großbritannien zur Seebaustelle übernimmt.
Nicht nur in der Nordsee, auch in der Ostsee entstehen große Windparks, beispielsweise EnBW Baltic 1 und 2. Bei Baltic 1, dem ersten kommerziellen Offshore-Windpark Deutschlands in der Ostsee, verfügen die 21 Windenergieanlagen über eine Gesamtleistung von 48,3 MW. Auf rund sieben Quadratkilometern werden jährlich etwa 185 Millionen Kilowattstunden Strom erzeugt, die den jährlichen Strombedarf von 50.000 Haushalten abdecken. Die Innerparkverkabelung besteht aus insgesamt 23 Kilometer 33-kV-Seekabeln. Die gesamte Trassenlänge der Stromleitungen beträgt rund 77 Kilometer, davon entfallen etwa 61 Kilometer auf die Seekabellänge und 16 Kilometer auf Landleitungen.
Deutlich größer ist der im September 2015 ans Netz gegangene Windpark Baltic 2, der 80 OWEA mit einer Gesamtleistung von 288 MW umfasst. Um die 80 Windkraftanlagen mit der Umspannstation zu verbinden, waren insgesamt rund 85 Kilometer Seekabel zu verlegen. Über diese Seekabel wird nicht nur der Strom transportiert, auch die Informationen und Daten zwischen den Anlagen und der Leitwarte in Barhöft werden über hochsensible Lichtwellenleiter ausgetauscht, die in die Kabel integriert sind. Ein spezielles Exportkabel transportiert dann den von 33 auf 150 kV transformierten Strom von der Umspannstation – via EnBW Baltic 1 – zum Umspannwerk Bentwisch an Land. Hier wird die Spannung von 150 auf 380 kV transformiert und die Einspeisung ins deutsche Verbundnetz vorgenommen. Die Kabellängen betragen etwa 120 Kilometer auf See und 16 Kilometer an Land.
Neben den Installationen der Umspannstation, der Fundamentstrukturen und der Windenergieanlagen zählt die Installation der Innerparkverkabelung bei Offshore-Windparks zu den größten Installationsschritten. Eine Studie von Uniconsult nennt anhand von Erfahrungs- bzw. Zielwerten die durchschnittlichen Installationszeiten für die einzelnen Großkomponenten des Offshore-Windparks. Danach werden als Installationszeit pro Fundament zwei Tage und pro Windanlage 1,5 Tage benötigt. Deutlich zeitaufwändiger ist die Installation der Umspannplattform, für die 70 Tage als Schätzwert benannt werden. Den größten Zeitaufwand erfordert aber die Verkabelung: pro Windpark sechs bis acht Monate.
Herstellung und Verlegung von Seekabeln
Offshore-Seekabel sind so genannte Dreileiterkabel. Nach Angaben der 50Hertz Transmission GmbH besteht jeder Einzelleiter aus dem eigentlichen Kupferleiter, der inneren und äußeren Leitschicht zur Steuerung der Felder sowie einer Hochspannungsisolierung aus vernetztem Polyethylen (VPE). Zur Datenübertragung von Mess- und Steuersignalen ist im Seekabel ein Glasfaserkabel integriert. Umhüllt wird der Kabelkern von verzinkten Stahldrähten zum Schutz gegen mechanische Schäden, zum Beispiel durch Schiffsanker. Die Seekabel werden für jede Verbindung individuell berechnet und angepasst. Sie haben einen Durchmesser von bis zu 25 Zentimeter und wiegen etwa 100 Kilogramm pro Meter.
Die Verlegung der Kabel im Meeresgrund stellt dem Unternehmen zufolge eine große Herausforderung dar: Die Kabel werden zunächst beim Hersteller auf große Kabeltrommeln aufgerollt, auf ein Kabellegeschiff verladen und auf die hohe See hinausgebracht. In Küstennähe wird das Kabel vom Schiff aus an Land gezogen. Schwimmkörper halten das Kabel für den Verlegevorgang an der Wasseroberfläche, damit es durch Steine und Unebenheiten auf dem Meeresboden nicht beschädigt wird. Ist das Kabel mit dem Verbindungspunkt an Land verknüpft, werden die Schwimmkörper entfernt und das Kabel sinkt langsam auf den Meeresgrund. Wenn das Schiff hinausfährt, rollt sich das Kabel von der Rolle ab und legt sich auf den Meeresboden. Das Kabelende wird mittels einer Muffe mit dem Kabelende der nächsten Kabellänge verbunden.
Je nach Beschaffenheit des Meeresbodens gibt es eine Vielzahl unterschiedlicher Legemethoden und Werkzeuge. Während zum Beispiel bei hartem und steinigem Meeresboden eher pflugähnliche Werkzeugschlitten zum Einsatz kommen, sind die Verhältnisse bei Sandboden sehr viel einfacher. Hier fährt ein Unterwasser-Spülschlitten über das gesamte Kabel und schafft eine metertiefe Rinne. Das Kabel sinkt in die Rinne und wird durch die Strömung auf dem Meeresboden eingeschlossen. Im letzten Schritt wird das Kabelende mit dem Transformator auf der Plattform verbunden. Das Legen eines 15 Kilometer langen Kabelabschnittes dauert etwa drei Tage. Wobei an vielen Stellen Unterwasserarbeiter, sprich Taucher, benötigt werden.
Zu den Herstellern von Offshore-Kabeln gehört mit Nexans Deutschland einer der nach eigenen Angaben führenden Kabelhersteller in Europa. Das Unternehmen liefert seit fast 30 Jahren weltweit aus dem Werk Hannover verschiedene Typen von VPE-isolierten Seekabeln. Der Kabelaufbau wird dabei durch die unterschiedlichen Anforderungen sowie Umgebungsbedingungen bestimmt und richtet sich dabei immer nach nationalen und internationalen Standards. Weil die Anforderungs- und Umgebungsprofile sehr differenziert sind, werden Seekabel projektspezifisch hergestellt.
Für die interne Windparkverkabelung eignen sich laut Nexans vor allem wartungsfreie 36-kV-VPE-Kabel mit integrierten Lichtwellenleiterelementen für die Datenkommunikation. Dazu gehören sowohl Kabelkonstruktionen mit als auch ohne Längs- und Querwasserschutz. Vorteilhaft sind Konstruktionen mit Aluminium-Schichtenmantel, denn sie haben ein geringeres Gewicht, kleinere Durchmesser und kleinere Biegeradien als Kabel mit Bleimänteln. Damit ist die Handhabung beim Verlegen und beim Einführen der Kabel in die Türme der Windkraft-Anlagen deutlich besser.
Bestens bewährt hat sich, so Nexans, die Stahl-Armierung. Die Verseilung der drei Energie-Kabel zusammen mit der darüber liegenden Stahl-Armierung ermöglicht es, die magnetischen Felder auf ein technisches Minimum zu reduzieren. Darüber hinaus stellt die Stahl-Armierung auch einen mechanischen Schutz der Kabel dar, der die enormen Zugkräfte bei der Verlegung und Befestigung in den Türmen aufnimmt.