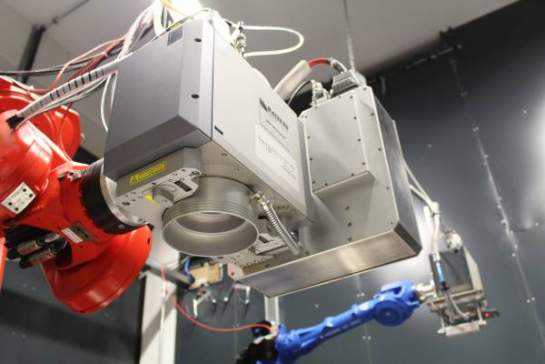
LASYS 2018: Produktivität hoch, Kosten runter – die Elektrofahrzeugfertigung profitiert von innovativen Laseranlagen
Die EVS30 (Electric Vehicle Symposium & Exhibition) war vom 9. bis 11. Oktober 2017 der Branchentreffpunkt für die gesamte Industrie der Elektromobilität. Hersteller, Anwender und Entscheider erhielten ein aktuelles Bild zu allen Formen der Elektromobilität und diskutierten neue Trends sowie Einsatzmöglichkeiten des elektrischen Antriebstrangs. In Stuttgart wurde gezeigt, wohin die Reise geht und keinen Zweifel daran gelassen, dass sich die Nachfrage nach Elektrofahrzeugen in Europa weiter steigern wird. Lasersysteme leisten durch neuartige, verbesserte wirtschaftliche Fertigungsverfahren einen wichtigen Beitrag und fördern so den Durchbruch der E-Mobilität. Das wird auch die nächste LASYS 2018 vom 5. bis 7. Juni 2018 widerspiegeln. Viele erfahrene Aussteller und Experten werden hier ihr Wissen über Innovationen und Lösungen zur Verfügung stellen.
Die internationale Fachmesse für Laser-Materialbearbeitung in Stuttgart hat sich zum wichtigsten Branchentreff für Lasersystemanbieter, Integratoren, Dienstleister und Laseranwender aus der Industrie entwickelt. Mit rund 200 Ausstellern geht die LASYS 2018 in die sechste Runde. Wegen ihrer hohen und breit gefächerten Anwenderorientierung spricht die Fachmesse sowohl den Maschinen- und Automobilbau, die Elektro- und Elektronikindustrie, die optische Industrie, den Anlagen- und Apparatebau, die metallbe- und -verarbeitende Industrie, die Medizintechnik, Kunststoffindustrie, den Werkzeug- und Formenbau sowie die Halbleiterindustrie und viele andere Branchen an.
Hohe Flexibilität und Produktivität durch den Einsatz von Lasersystemen
Pionier im Einsatz von Lasersystemen war von jeher der Automobilbau. Ein aktuelles Trendthema sind Elektrofahrzeuge und deren Akzeptanz. Leistungssteigerung und Kostenreduktion stehen hier auf dem Plan. Eine der großen Herausforderungen sieht Marc Kirchhoff, Leiter Branchenmanagement Automotive bei Trumpf, diesbezüglich im Aufbau von Produktionskapazitäten im automobilen Maßstab, das heißt in hohen Stückzahlen. „Aufgrund seiner hohen Produktivität und Flexibilität ist der Laser hierfür das ideale Werkzeug“, sagt er. „Die Anwendung des Lasers zieht sich durch die gesamte Prozesskette der Elektroautomobilfertigung“, so Dr. Jens Standfuß, Leiter des Geschäftsfelds Fügen beim Fraunhofer Institut für Werkstoff und Strahltechnik (IWS) in Dresden, „ganz gleich, ob es die Batterieherstellung, elektrische Kontaktierungen, Verbindungen oder den Antriebsstrang – also Leistungselektronik und Elektromotor – betrifft.“ Das IWS sowie Trumpf werden als Aussteller auf der LASYS 2018 präsent sein.
Batterien durch Oberflächenstrukturierung noch leistungsfähiger machen
Allein bei der Herstellung der Batterie ist der Laser mittlerweile unverzichtbar. Das IWS erforscht unter anderem in Richtung Batteriezellen zweiter Generation. „Mit dem Laser verbessern wir über direkt strukturierende Verfahren oder Interferenzverfahren die Oberflächeneigenschaften von Elektrodenfolien. Auf diese Weise lassen sich in Abhängigkeit von der Wellenlänge und Pulsenergie Strukturen im Mikro- bzw. Submikrometermaßstab erzeugen. Im Zusammenhang mit optimierten Beschichtungssystemen und der Zellchemie können wir letztendlich die gravimetrische Energiedichte erhöhen und Materialkosten senken“, erklärt Dr. Standfuß. Das bedeutet, die Batterie wird leistungsfähiger und man kann längere Strecken mit dem Elektroauto zurücklegen. Das E-Mobil wird somit noch attraktiver für Autofahrer.
Scanner plus Bildsensoren ermöglichen schlanke Fertigungsstationen
Es gibt noch weitere Prozessschritte, die der Laser bei der Batterieherstellung hervorragend meistert. Trumpf-Experte Kirchhoff berichtet: „Laser lassen sich einsetzen, um den Rahmen, der das Batteriezellenpaket umgibt, verzugsarm und damit vorteilhaft für die Wärmeleitung zu schweißen. Ebenso sind Laser heute das Standardwerkzeug, um prismatische Batteriezellen zu verschließen und diese danach auf Modulebene untereinander zu kontaktieren.“ Thibault Bautze, Leiter Technischer Vertrieb Blackbird Robotersysteme, konstatiert: „Gerade im Bereich der Elektromobilität ist für eine Vielzahl von Anwendungen eine stoffschlüssige Verbindung unterschiedlicher Materialien, wie etwa zwischen Kupfer und Aluminium, als Ersatz für mechanisch gefügte Verbindungen interessant.“ Statt verschraubt, wird nun die Aluminiumelektrode mit der Kupferableitung verschweißt. „Dank des sehr gut fokussierbaren Lasers“, so Bautze weiter, „ lässt sich die Leistung zum Aufschmelzen mit einer sehr hohen Leistungsdichte in das Bauteil einbringen.“ Dadurch könne die Schweißnaht hochgenau platziert werden. Dies erlaube einerseits die Bearbeitung sehr kleiner Bauteile, andererseits könne dem Blackbird-Experten zufolge trotzdem ein Abstand zu wärmeempfindlichen Materialien, wie Kunststoffen, eingehalten werden. „Vorteile sind unter anderem eine verbesserte elektrische Leitfähigkeit der Kontaktierung, ein gleichmäßiger Wärmeübergang und höhere mechanische Belastbarkeit“, erläutert Bautze. Er fährt fort: „Bei diesem Materialmix kann der Laser, vor allem in Verbindung mit einem Scanner, seine ganzen Vorteile beim Laserschweißen aufzeigen. In Kombination mit Bildsensoren zur Bauteillageerfassung sind sehr kurze Taktzeiten und schlanke Fertigungsstationen realisierbar, die mit konventionellen Fügeverfahren nicht erzielbar wären.“ Auch die Experten von Blackbird Robotersysteme unterstützen die LASYS-Besucher gern mit ihrer Fachkompetenz und ihren Exponaten.
Aluminium und Kupfer fordern Lasersysteme heraus
Aluminium und Kupfer sind Materialien, die das Licht sehr stark reflektieren. Deshalb sind Hersteller hier ganz besonders herausgefordert, Lasersysteme zu entwickeln, die effizient Photonenenergie in das Material einbringen. „Wir testen zusammen mit Strahlquellenherstellern Laser, die im Wellenlängenspektrum grün sowie blau arbeiten“, sagt Dr. Standfuß. Trumpf-Experte Kirchhoff stellt fest: „Neue Strahlformungskonzepte oder veränderte Wellenlängen wie grünes Laserlicht, reduzieren auch signifikant die Anzahl der Spritzer beim Schweißen von Kupferbauteilen.“
Leichtbauweise profitiert von Vielseitigkeit des Lasers
Leichtbauweise ist schon seit einigen Jahren in aller Munde, wenn es um die Automobilproduktion geht. Gerade auch bei Elektroautos spielt sie eine wichtige Rolle. „Durch Leichtbau soll zum einen das hohe Gewicht der Batterieelemente kompensiert und zum anderen die nötigte Antriebsenergie reduziert werden. Hier kann der Laser zum Fügen und Schneiden neuartiger Materialien für den Leichtbau eingesetzt werden“, betont Georg Hofner, Sprecher der Geschäftsführung von SCANLAB. Doch er sieht noch weitere Laserapplikationen wie die Bauteilreinigung vor dem Kleben oder Schweißen und auch Härten von Bauteilen. „Diese Vielseitigkeit des Lasers ist für zukünftige Leichtbaumaterialien eine Notwendigkeit, um wirtschaftlich fertigen zu können“, so Hofner weiter. Auch SCANLAB wird als Aussteller der LASYS 2018 mit Innovationen und Expertenwissen den Messebesucher bei Problemlösungen unterstützen.
Dank Laser, Wirkungsgrad des Elektromotors erhöhen
Bereits jetzt schon und in Zukunft wird der Laser bei der Fertigung der Elektromotoren eine wesentliche Rolle spielen. Kirchhoff meint: „Laser werden eingesetzt, um beispielsweise Hair-Pins in Elektroantrieben remote zu verschweißen, berührungsfrei – und dank Bildverarbeitung hochpräzise.“ Neuentwicklungen, die derzeit im Bereich der Automobilindustrie laufen, betreffen beispielsweise die Elektrobleche für die Rotoren. Auch das IWS engagiert sich auf diesem Gebiet: „Zum einen lassen sich Bleche mit Lasern wesentlich günstiger zuschneiden“, erklärt Dr. Standfuß, „zum anderen kann man damit die elektromagnetischen Verluste reduzieren. Die Schneidgeschwindigkeiten mit Lasern sind so hoch, dass letztlich die beeinflusste Zone entlang der Schnittkante deutlich kleiner ist, als es bei mechanischen Stanzverfahren der Fall ist. Das wirkt sich auf die Ummagnetisierungsverluste und auf den elektrischen Wirkungsgrad des Motors aus.“ Auch über eine optimierte Lamellengeometrie sowie über gezieltes Laser-Strukturieren zum Verbessern des elektromagnetischen Verhaltens ließen sich zukünftig effizientere Motoren bauen. Lasersysteme sind frei programmierbar, was zum Beispiel die Schnittgeometrie von Lamellen angeht. Gerade in der Anfangsphase einer neuen Produktreihe spiele dem Forscher zufolge das Thema „Stückzahl und Kosten“ eine große Rolle. „Ein Stanzwerkzeug ist mit hohem Aufwand verbunden, der dann auf die Anzahl der Produkte umgelegt werden muss. Hier zahlt sich die Flexibilität des Lasers auch in Zukunft sicherlich noch aus“, resümiert Dr. Jens Standfuß. Die E-Mobilität ist somit auch ein bedeutender Wachstumstreiber für Laseranwendungen.
Rahmenprogramm auf höchstem Niveau
Die kommende LASYS verspricht spannend zu werden. Laser-Materialbearbeitung in allen Facetten erwartet die Fachbesucher auf dem Stuttgarter Messegelände. Und das praxisorientierte, hochkarätige Begleitprogramm zur LASYS 2018, wie beispielsweise die Stuttgarter Lasertage (SLT), das Fachforum „Lasers in Action“ oder der „Stuttgart Laser Marketplace“, bieten internationalen Wissensaustausch auf höchstem Niveau. Ein weiterer Grund, im Juni 2018 nach Stuttgart zu kommen.